Seven Servo Motors Drive High Speed Paper Cup Machine MYC-160S
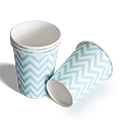
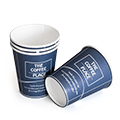
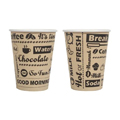
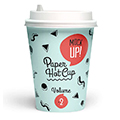




Machine | MYC-160S Seven Servo Motors Drive High Speed Paper Cup Machine |
Cup Side Welding | Ultrasonic heater |
Cup Size | 1.5 ~16 OZ (Mould exchangeable, Max Cup Height: 136mm , Max Bottom width: 80mm) |
Rated Speed | 140-160pcs/min |
Raw Material | One or Two side PE coated Paper, PLA paper, Aluminum foil, Plastic-free paper (Popular for Hot and Cold drink Cups) |
Suitable Paper Weight | 140g-350g |
Total Power | 20KW(Stable Runnung Consumption 12KW) |
Total Weight | 3000 kgs(machine)+100kgs (cup-collecting device) |
Package Size (L*W*H) | 3230×1750×2250mm |
Power Source | 50/60HZ, 380V/220V(better use 380V,3 Phase ) or special power requirement |
Working Air Source | Air pressure:0.6Mpa Air Out-put:0.5m³/min Need to buy Air Compressor (by user) |
Our engineer team will send the operation video to guide you tcsolve the problem .if the spare parts is broken in the warrantyperiod, we will send you the new replacement parts for frec.
Raw materials : Single /double PE coated paper fan which isalready cut and printed , bottom paper roll
PS: Machine is without printing and cutting function(onlycan cut bottom roll paper, it can not cut the paper fan )
One machine is installed one full set mould for free. You canbuy extra half set mould (easy to change) or full set mould(difficult :1% success rate). We only recommend to change1-3 sets half set mould (with same bottom diameter size)in one machine.
Food grade or silicone oil and a small air compressor.
The machine will be finished installation and tested runningperfectly before the delivery . You will get the completemachine which is finished installation. We will provide the fulloperation and training Videos to guide you to run the machineAnyone can install the machine and operate it easily.
Through this video, we will show you the paper cup manufacturing processand superior performance of MYC-160S. This machine can produce cupsranging from 1.5 to 16 ounces, meeting various size requirements.
More videos
|
7 Pcs of sensor-Panasonic Sensor It can detect the full working process of the machine like paper less, paper stuck, paper tube blocking, hot air blowing, bottom paper feeding and cup passing by errors. It wil send alarm and ensure machine inside spare parts less collision issues, and run more stable |
|
7 Pcs of sensor-Others Less sensors only 6 pcs, machine running process will cause some issues and finished cups will be not good. |
|
Automatic Paper Fans Feeding Unit Feeding the paper fan automatically and save labor costs. |
|
Single Rotating Paper Suction Unit Precise control of paper suction output stability. make the paper fan feeding smoothly by transferring directly into the runway to avoid the problem of paper jam. |
|
Hot Air Paper Fan Pre-heater Hot air paper fan pre-heaters are in both side and the paper fan ispre-heated by the hot air pre-heater which can ensure the better welding effect(no leakage issues) before ultrasonic sealing when machine is running at high speed. |
|
UItrasonic And Heater Together For The Mid Sealing Our machine will has both ultrasonic and hot air heating for making the mid sealing of the cup. |
|
Double Turnplate Design Top rim curling and bottom sealing in separated turnplate which can greatly improve the machine stable. |
|
Integral Mould Head The whole mold head with 10pcs and adopt aluminum material compare with the single plate only 8pcs bakelite separable material,the finished paper cup not easy be dirty. |
|
Two Times Top Curling Unit (With Heater) We use two times rim rolling design. Roling the rim two times and make the cup rim harder,the edge will goes inside deeper,the rim will not open easily. |
|
3 PCS Bottom Hot Air Pre-heaters 1 hot air bottom paper folding heater, and 2 pcs bottomhot air pre-heaters can ensure bottom sealing no leakages issuesin high speed. |
|
Bottom Waste Conveyor Bottom paper will be transferred by the converyor and go outess bottom waster paper stucking issues. |